開発者インタビュー
第2回 課題&克服:
ASKA3D商品化への道のり
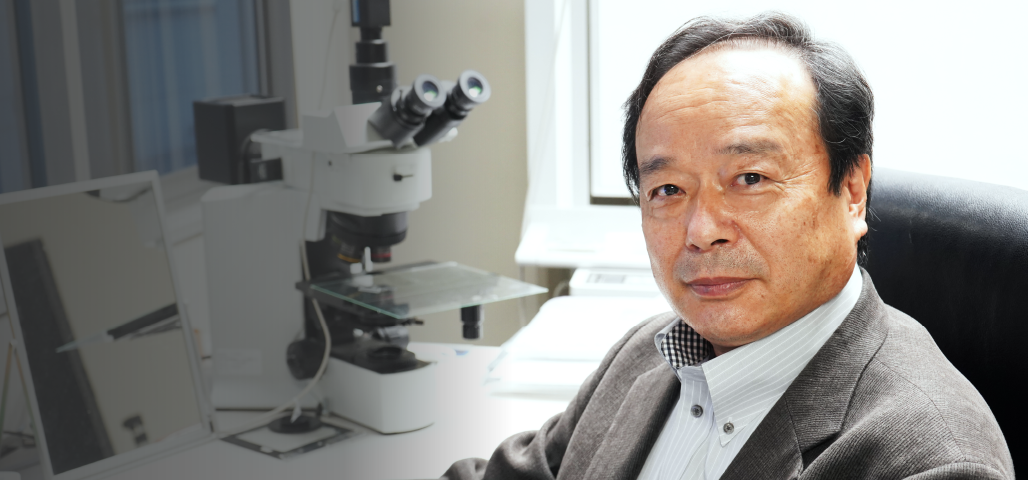
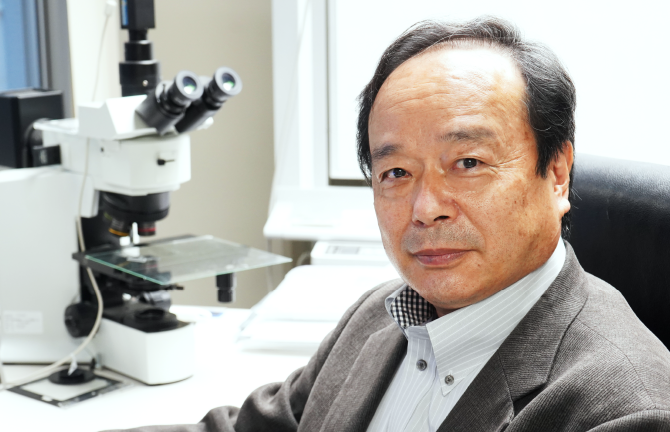
株式会社アスカネット空中ディスプレイ開発者
大坪 誠
Otsubo Makoto
アスカネットへの参画とプロトタイプの開発
前回のインタビューでは、空中ディスプレイの着想からアスカネットに参画する直前までのお話を伺いました。アスカネット参画当時の状況を教えてください。
アスカネットに参画したのは2011年3月でした。大分から広島への引越し作業中に東日本大震災が発生した時で、当時のことをよく覚えています。
アスカネットでは当事業の担当役員、マネージャー、開発者である私の3人体制で事業をスタートしました。
最初のミッションは福田社長(アスカネット創業者2020年に会長職を任期満了退任)と前任の会社の製造委託先に継続取引を求めて全国行脚をすることでした。
特に基礎的な開発をしてもらっていたところを中心に回り、交渉は非常にスムーズだったと記憶しています。
ASKA3Dの基礎開発とは、具体的にどのようなものでしょうか。
ASKA3Dの空中ディスプレイは、今まで世の中に存在しなかったものです。直交ミラーの原理で実現出来ることは幾何学的に分かっていたのですが、実際のプロダクトとして製造するのはたくさんの研究開発が必要でした。
素材の選定にはじまり、接着剤の成分、蒸着の方法、構造上の問題など、未知の問題にゼロから手探りで取り組み、カタチになるところまでが基礎開発と言えます。
当時のASKA3Dプレートはどのようなものでしたか?
最初は小さなサイズからの開発で、150mm角でした。
このサイズから開始したのは、当時の研磨装置のサイズにちょうど合うからです。
マネージャーも一緒に製造委託先を訪問し、この150mm角の今後の製品化・量産化に取り組むコンセンサスを得る営業活動も行いました。アスカネット入社以前は開発だけでなく営業活動や資金繰りなど、ほとんど一人で行っていましたので、マネージャーの存在は大変心強かったです。
前述の基礎開発は2011年の時点でほぼクリア出来ていましたが、映像が暗いという大きな課題がありました。
空中映像は45度の角度にスイートスポットがあるのですが、その角度で見て非常に空中映像が暗かったのです。入社した2011年の秋には展示会への初出展が決まっていたので、どうしてもこの明るさの問題を急ぎ解決する必要がありました。
空中映像の明るさに課題があったとのことですが、アスカネット入社時はまだ暗い空中映像だったのですね。
私としても明るさが不安点だったので、役員へのデモンストレーションの際に高輝度のプロジェクターから直接光を当てて空中映像をお見せするなど工夫しました。当時の一般的なディスプレイでは空中ディスプレイとして商品化できるビジョンが見えなかったのです。
実はアスカネットに採用いただく際に2回プレゼンを行っており、1回目は不採用でした。
幸い福田社長から2回目のプレゼン機会をいただき、アスカネットでの開発のチャンスをいただけました。
また入社後、この明るさの問題はミラーのピッチと高さのアスペクト比を調整することで無事解決し、何とか秋の展示会に間に合いました。
展示会初出展とアスカネットでの大きな前進
展示会の初出展(サイン&ディスプレイショウ2011)ではどのような反応がありましたか?
アスカネットに参画する前は、展示会のような大規模な場面で空中ディスプレイを見てもらう機会はありませんでした。
そのため最初の展示会では非常に反応が大きかったです。世の中に全くないものであったため衆目を集め、相当な大手企業からベンチャー企業、大学、企業の研究機関など様々な団体からご関心いただきました。
しかしながら、出展したASKA3Dプレートはまだまだアーリーステージで、サンプル・プロトタイプレベルのものでした。
もちろん製造体制の構築も出来ておらず、少量作れた中で一番良いサンプルで展示会に出展したのです。
組み込みの用途を模索したい企業も多く基礎研究用のサンプルをご所望いただいたのですが、当時は数が作れない故に1点があまりに高額であったため、お応えすることが出来ず残念な思いをしました。
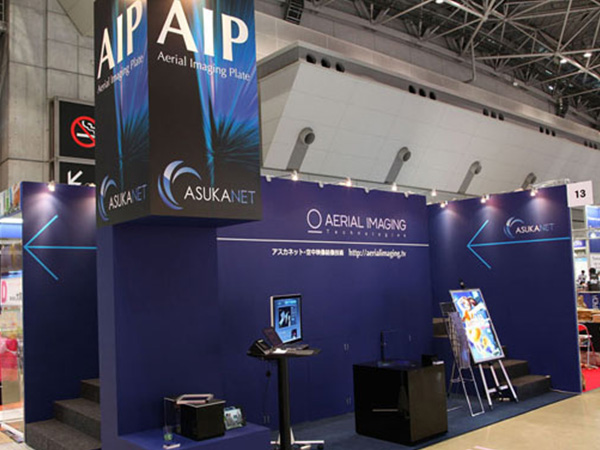
サイン&ディスプレイショウ2011 展示ブース
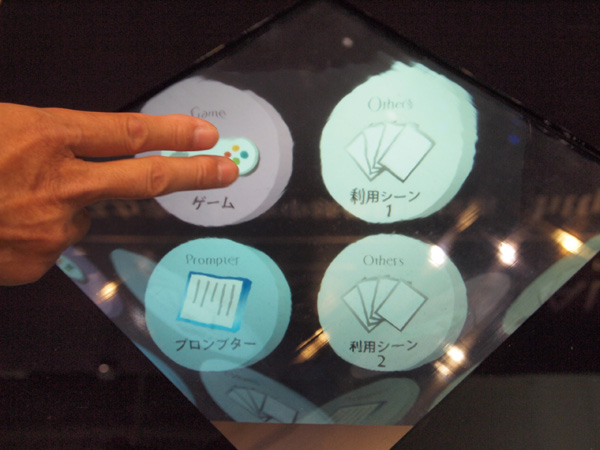
サイン&ディスプレイショウ2011 展示品
その後の活動について教えてください。
展示会にも無事初出展出来たので、いかに品質を保持したまま安く大量につくれるかというミッションを持って量産化開発に着手しました。会社から十分な予算を確保してもらい、思い切った開発が出来ました。
京都の会社や広島の会社と共同研究に取り組み、協力先の技術者と一丸となって開発目標を達成する。それによりコアコンピタンスを獲得することが第一目標でした。
また、150mm角製造のローコスト化、社会に空中ディスプレイを知ってもらうための取り組みも同時並行で行いました。
CEATECをはじめとする展示会出展での認知活動が出来たのは、アスカネットの資本があったからこそだと思います。
お陰様でCEATEC JAPAN 2013ではキーテクノロジー部門の準グランプリを受賞し、一気に認知も広まりました。
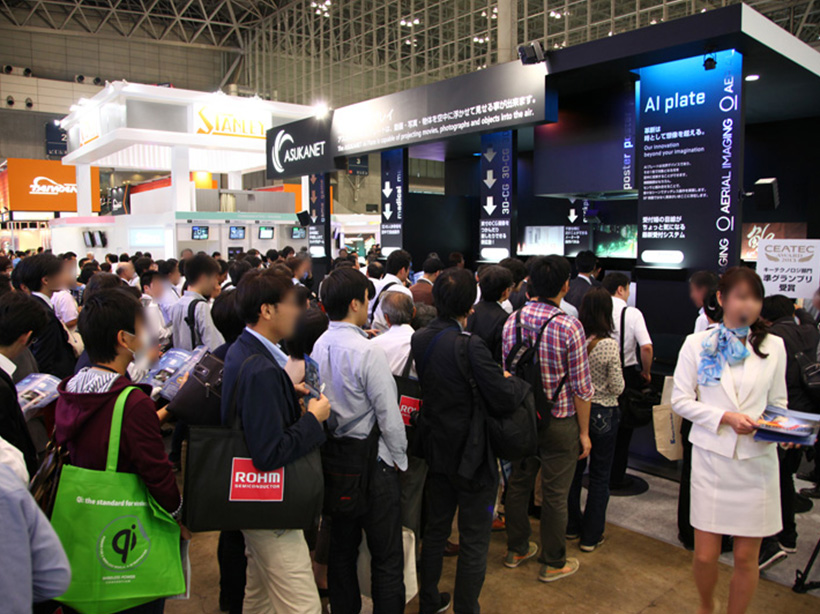
CEATEC JAPAN 2013 展示ブース
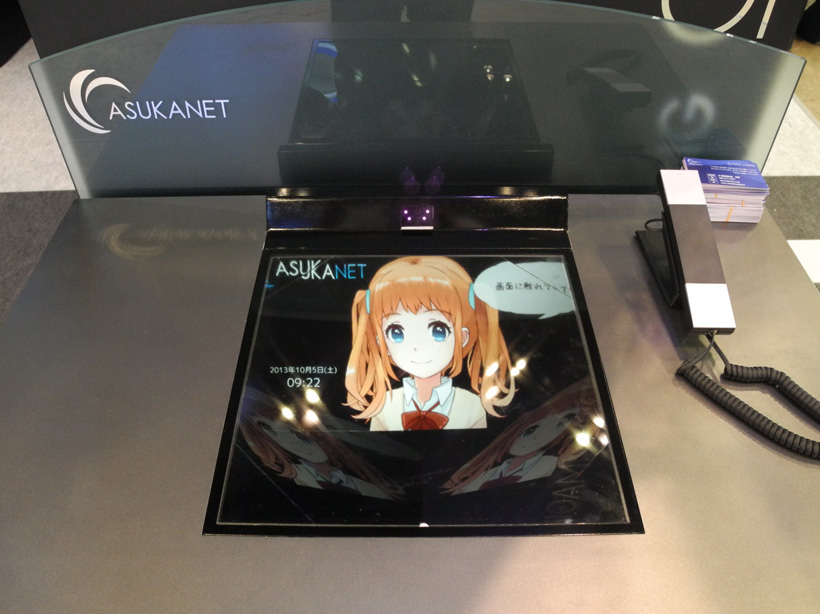
CEATEC JAPAN 2013 展示品
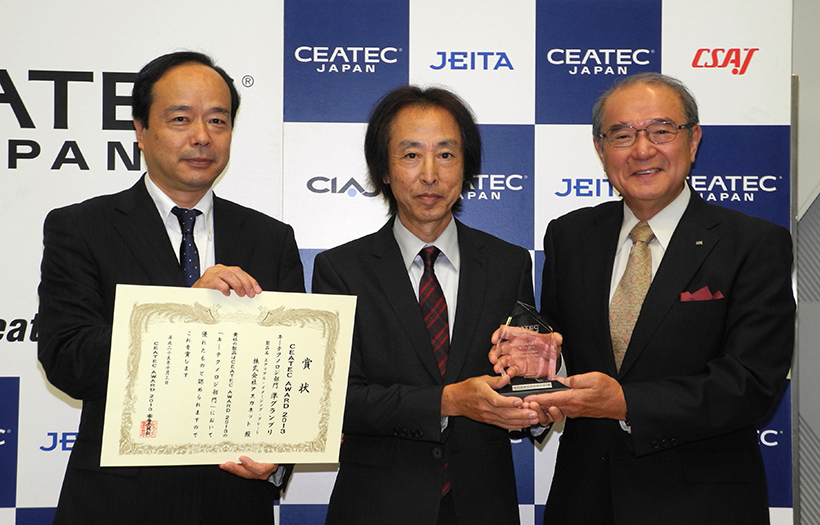
独自の技術 CEATEC AWARD2013 キーテクノロジー部門 準グランプリ受賞
アスカネットに参画以降、ASKA3Dの空中ディスプレイは大きく実現に向けて動いたようですね。
要因はどこにあったのでしょうか。
一番は潤沢な開発予算です。前任の会社ではなるべく無駄を削いで、根本的な部分の開発・検証にフォーカスしていました。
そのままではベンチャー企業としての技術発表会止まりで、商品化への道のりは険しかったと思います。
過去の下地があり、アスカネット参画後十分な予算を組んでいただいたので、商品化に向けて加速度的にスピードアップすることが出来ました。
二つ目は前述の明るさ問題を解決出来たことです。
アスペクト比による課題解決で空中映像の実用に耐えうる明るさを実現出来たため、一般的なモニターで十分商品化出来る空中映像が実現しました。プロジェクターで無理やり輝度を確保していたことを考えると、この進捗は大きかったです。
アスカネット参画後は資金繰りや営業活動にとらわれず、開発に専念できる環境を用意いただけたのも功を奏しました。
様々な課題と克服への挑戦
ASKA3Dの商品化までにはどのような課題を克服していったのでしょうか。技術面でも教えてください。
手探り状態からのスタートでしたが、まずはアーリー・ミドルス・ビジネスステージという事業計画をたて、最初の2~3年間はアーリーステージとしてプロトタイプを作り、お客様の要望に答えられるもの作りに専念しました。
製造委託先と共同開発を繰り返して、プロトタイプに力を入れていく方針です。
プロトタイプの開発にある程度の目処が立つと、空中ディスプレイの「サイズアップ」の課題が出てきました。
ASKA3Dプレートをサイズアップすると、構造上・光学上の両面でどんどん課題が表面化し、商品化のハードルが上がります。
具体的には、結像の歪みへの対応がサイズアップの課題でした。
光は距離の二乗に比例して球面状に拡散します。自然光のベクトル成分を正確に変換しない限り、拡散の途中に入る空間フィルター(ASKA3D)は結像の歪みとして影響を及ぼします。
フィルターの精度次第で、距離の二乗に比例してどんどん結像が歪んでいくのです。
小さなサイズのASKA3Dプレートは結像距離が短いので、歪みは少なく目立ちません。
サイズアップをすると結像距離が遠くなるため、歪みも大きくなるのです。
現在のガラス製ASKA3Dではこの歪みの問題は大きく改善していますが、完璧に歪みを無くすには結像素子レベルのインプルーブが必要で、熱膨張係数がゼロに近いガラスを利用するなど、別のより高コストなアプローチが必要となります。
空中ディスプレイのサイズアップは、ASKA3Dを大きく作れば良い、という簡単な話ではないのですね。
その通りです。他にも結像上の課題としては「ボケ」や「輝度の低下」がありました。
またプレートの外観上も「反り」「製造時の割れ・欠け」「白霞」「黒筋模様」「ミラー抜け」など精度の問題が発生し、それらは全て空中映像の品質に大きく影響します。
ASKA3Dは当初より、現実的なコストで安定供給を出来るよう、世に流通しているスタンダードなガラスで製品化することを試みています。なのでこれらの課題は素材の問題ではなく、加工の問題として解決が必要でした。
結像・プレート外観の課題に対し、都度製造委託先の技術者と研究を重ね、試作を繰り返すことで検証し、これらの課題を一つずつ克服してきました。
ちょっとした人為的なミスや、傷やホコリが入っただけでも大きな損失に繋がるのが製造ラインの難しいところです。
ここ数年の技術や治具の最適化で、製造技術・精度については限界点に到達することが出来ました。
現在は素材による様々な課題の解決に取り組んでおります。
まさに課題の発見と克服を繰り返すことで商品化、ひいては現在の品質にたどり着いたのですね。
商品リリースから現在までの、ASKA3Dプレートの進化について教えてください。
初期は小サイズ商品化までの4年間は初期・サンプル段階でした。
単板150mm角
中期は次の4年間、中型サイズ商品化の挑戦でした。
単板345mm角、タイリング品488mm角、976mm角の開発、商品化です。
サイズアップをタイリングで実現する方針に切り替え、単板の精度とタイリング技術の向上に務めました。
後期(現在までの4年間)は大型サイズの商品化に取り組みました。
タイリング品488mm角、1,050mm角を実現しています。
繰り返しになりますが、同じ素材でも距離の二乗に比例して結像に歪みが生じるという縛りの中での開発です。
タイリングにも映像の歪みやズレが課題となりますし、光学的なデバイスのため、三次元的なアライメントとの戦いの歴史とも言えます。
いかにフラットに、三次元的なアライメントを取るか。要素基盤の厚みがミクロン単位で厚い・薄いだけで大きく精度が下がるのです。
1,000mmを超える大型化は要素基盤の精度向上に大きな苦労を伴ったため、委託先の協力無しには実現出来なかったと思います。
「映像がASKA3Dにより空中に結像する」という現象や基本的な原理はアスカネット参画当時より一環していますが、その加工技術、製造方法は研究開発とたゆまぬ課題解決への努力により、大きく進化してきました。
今回はアスカネット参画後、ASKA3Dがどのような課題を克服しながら商品化、現在の品質にたどり着いたのかをお聞きしました。
次回は【未来を描く光 ASKA3Dが拓く新しい日常】について伺います。